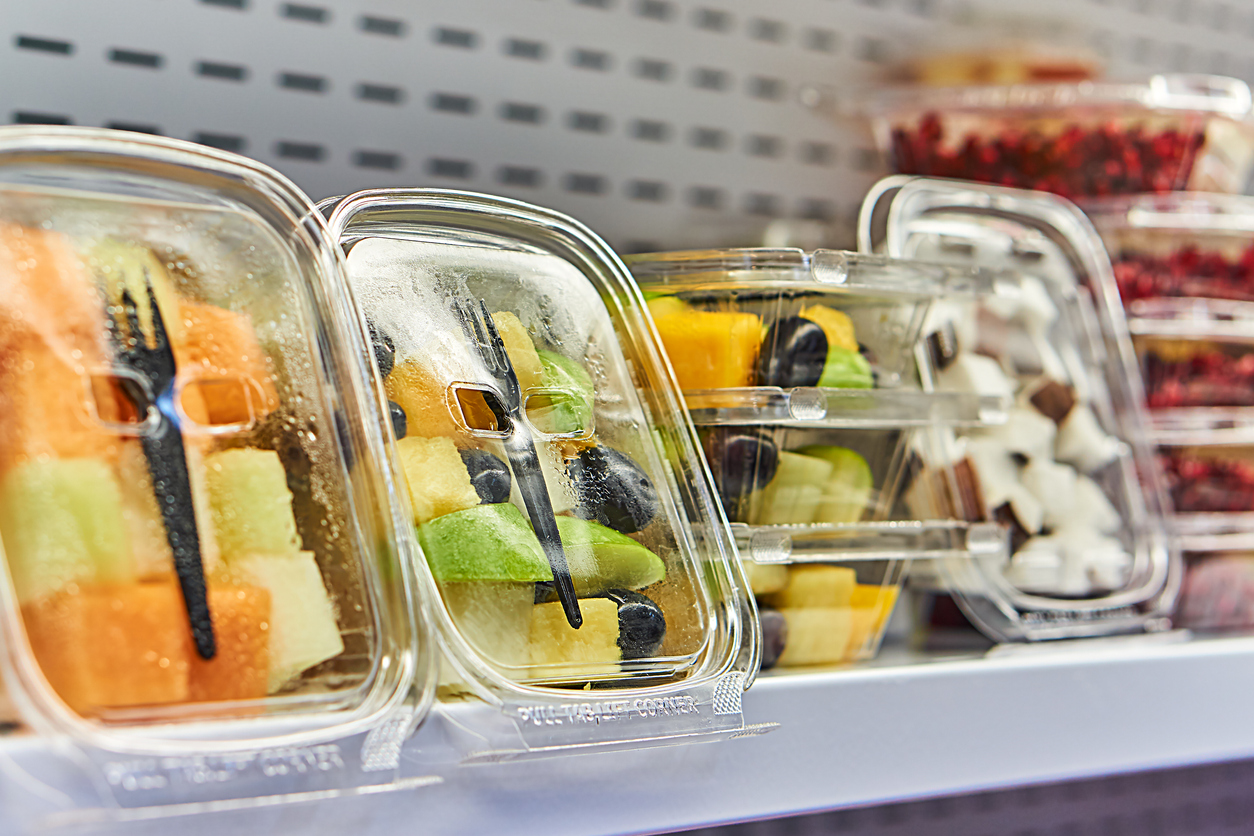
Plastics can be defined as: organic macromolecular compounds obtained by polymerisation, polycondensation, polyaddition or any similar process from molecules with a lower molecular weight or by chemical alteration of natural macromolecular compounds. Plastic packaging is used to protect goods during transportation, distribution and storage. Examples of plastic packaging include bags, bottles, jugs, clamshells, trays, cartons, baskets, containers, cases, plastic film packaging, and tubes.
Plastics are widely used for packaging materials and in the construction of food processing plant and equipment, because:
- they are flowable and mouldable (under certain conditions), to make sheets, shapes and structures
- they are generally chemically inert, though not necessarily impermeable
- they are cost effective in meeting market needs
- they are lightweight
- they provide choices in respect of transparency, colour, heat sealing, heat resistance and barrier properties
The first plastics were derived from natural raw materials and, subsequently, in the first half of the twentieth century, from coal, oil and natural gas. Polyethylene, the most widely used plastic today, was invented in 1933 and was used in packaging from the late 1940s onwards in the form of squeeze bottles, crates for fish (replacing wooden boxes) and film and extrusion coatings on paper-board for milk cartons.
Most packaging plastics are thermoplastic, which means that they can be repeatedly softened and melted when heated. This feature has several important implications for the use and performance of plastics, as in the forming of containers, film manufacture and heat sealability.
Thermosetting plastics are materials that can be moulded only once by heat and pressure. They cannot be re-softened, as reheating will cause the material to degrade. Thermosetting plastics, such as phenol formaldehyde and urea formaldehyde, are used for threaded closures in cosmetics, toiletries and pharmaceutical packaging but are not used to any great extent for food packaging.
Types of plastics used in food packaging
The following are the types of plastics used in food-packaging:
Polyethylene (PE)
PE is structurally the simplest plastic and is made by addition polymerization of ethylene gas in a high temperature and pressure reactor. Polyethylene are readily heat sealable. They can be made into strong, tough films, with a good barrier to moisture and water vapour. They are not a particularly high barrier to oils and fats or gases, such as carbon dioxide and oxygen compared with other plastics, although barrier properties increase with density. It includes low-density polyethylene (LDPE) and high-density polyethylene (HDPE) HDPE is used to make milk jugs and bottles for consumer products and also has numerous non-packaging applications, from trash bins to medical devices. LDPE is often used for bags and wraps, while HDPE is commonly found in milk jugs and detergent bottles.
Major uses of PE film are in shrink and stretch wrapping for collating groups of packs and for securing pallet size loads.
Polypropylene (PP)
PP is an addition polymer of propylene formed under heat and pressure using Ziegler-Natta type catalysts to produce a linear polymer with protruding methyl (CH2) groups. The resultant polymer is a harder and denser resin than PE and more transparent in its natural form. PP has the lowest density and the highest melting point of all the high volume usage thermoplastics and has a relatively low cost. This versatile plastic can be processed in many ways and has many food packaging applications in both flexible film and rigid form. The high melting point of PP (160◦C) makes it suitable for applications where thermal resistance is needed, for example in hot filling and microwave packaging.
The range of food products packed in PP films include biscuits, crisps (chips) and snack foods, chocolate and sugar confectionery, ice cream and frozen food, tea and coffee. Metallized PP film can be used for snacks and crisps (chips) where either a higher barrier or longer shelf life is required.
Polyesters (PET, PEN, PC) (Note: PET is referred to as PETE in some markets)
Polyesters are condensation polymers formed from ester monomers, resulting from the reaction of a carboxylic acid with an alcohol. There are many different types of polyester, depending on the monomers used. When terephthalic acid reacts with ethylene glycol and polymerizes, the result is PET.
PET can be made into film by blowing or casting. It can be blow moulded, injection moulded, foamed, extrusion coated on paperboard and extruded as sheet for thermoforming.
Polyesters have much higher heat resistance than many plastics and, when oriented, have very high mechanical strength.
PET is a medium oxygen barrier on its own but becomes a high barrier to oxygen and water vapour when metallized with aluminum. This is used for vacuumed coffee and bag-in-box liquids, where it is laminated with EVA on both sides to produce highly effective seals. It is also used in snack food flexible packaging for products with a high fat content, requiring barriers to oxygen and ultra violet (UV) light. Metallized PET, either as a strip or as a flexible laminate, is used as a susceptor in microwaveable packaging.
Polycarbonate (PC)
PC is a polyester containing carbonate groups in its structure. It is formed by the polymerization of the sodium salt of bisphenolic acid with phosgene. PC is mainly used as a glass replacement in processing equipment and for glazing applications. Its use in packaging is mainly for large, returnable/refillable 3–6 L water bottles. It is used for sterilisable baby feeding bottles and as a replacement in food service. It has been used for returnable milk bottles, ovenable trays for frozen food and if co-extruded with nylon could be used for carbonated drinks.
Polyvinyl chloride (PVC)
If one of the hydrogen atoms in ethylene is replaced with a chlorine atom, the resultant molecule is called vinyl chloride monomer (VCM). Addition polymerization of vinyl chloride produces PVC. PVC has excellent resistance to fat and oil. It can be used in the form of blow moulded bottles for vegetable oil and fruit drinks. It has good clarity. As a film, it is tough, with high elongation, though with relatively low tensile and tear strength. The moisture vapour transmission rate is relatively high, though adequate for the packaging of mineral water, fruit juice and fruit drinks in bottles.
Polystyrene (PS)
PS is an addition polymer of styrene, a vinyl compound where a hydrogen atom is replaced with a benzene ring. PS has many packaging uses and can be extruded as a monolayer plastic film, co-extruded as a thermoformable plastic sheet; injection moulded and foamed to give a range of pack types. It is also co-polymerized to extend its properties.PS so far described is general purpose polystyrene. The main disadvantage as a rigid or semi-rigid container is the fact that it is brittle. This can be overcome by blending with styrene butadiene co-polymer, SB or SBC, an elastomeric polymer. Blending produces a tougher material. It is translucent and is often used in a white pigmented form.
Foods Recommended to Store in Plastic Packaging
Certain types of food are well-suited for storage in plastic packaging due to their compatibility with the materials used:
Fruits and Vegetables: Many fruits and vegetables can be stored in plastic bags or containers that allow for some ventilation to prevent moisture buildup while maintaining freshness.
Dairy Products: Items like cheese or yogurt are often packaged in plastic due to its ability to create a moisture barrier that helps preserve freshness.
Processed Foods: Snacks such as chips or crackers are typically packaged in plastic bags that protect them from air exposure which could lead to staleness.
Frozen Foods: Plastic packaging designed for freezing helps maintain the quality of frozen meals by preventing freezer burn through airtight seals.
Condiments: Many sauces and dressings are stored in plastic bottles or jars because they are lightweight, shatterproof, and easy to dispense.
Foods Not Recommended to Store in Plastic Packaging
While many foods benefit from plastic packaging, there are certain items where caution should be exercised:
Fatty Foods: Items high in fat content can interact with certain plastics leading to leaching of harmful substances like phthalates or BPA into the food.
Hot Foods: Storing hot foods directly in plastic containers can cause the release of toxic chemicals from the plastic into the food; therefore, it’s advisable to let food cool before transferring it into plastic storage.
Acidic Foods: Foods like tomatoes or citrus fruits can react with certain types of plastics (especially PVC), leading to chemical leaching which may pose health risks.
Alcoholic Beverages: Storing alcoholic beverages in plastic can lead to degradation of both the container material and the beverage itself over time due to chemical interactions.
Food Intended for Long-Term Storage: Items meant for long-term preservation should ideally be stored in glass or metal containers rather than plastic due to concerns about chemical leaching over extended periods.
Effects of Plastic Packaging on Health and Environment
The use of plastic packaging presents several health concerns primarily related to chemical leaching into food products: Chemicals such as Bisphenol A (BPA) have been linked with hormonal disruptions when they migrate from plastics into food. Phthalates found in some plastics may also pose health risks including reproductive issues.
From an environmental perspective:
The production process contributes significantly to greenhouse gas emissions. Plastics take hundreds of years to decompose, leading to pollution that affects wildlife and ecosystems. Recycling rates remain low globally; thus much plastic ends up in landfills or oceans contributing further to environmental degradation.
In conclusion, while plastic packaging offers convenience and protection for many types of foods, careful consideration must be given regarding what foods are stored within these materials due to potential health risks associated with chemical leaching as well as broader environmental implications.